Picking is a very laborious and time-consuming part of order fulfillment. Fortunately, there are a variety of methods you may employ to improve your selection process through the strategic use of manpower and other forms of material handling technology. It's crucial to make sure you're employing the best picking approach for your company before investing in technology or automation to back up your choosing processes and cut costs.
Unfortunately, there is no universally optimal picking technique. When deciding on a warehouse picking strategy, you should think about your order profile, material flow, the physical layout of the facility, the number of line items in an order, the availability of workers, and how/when orders are released by your management system. What does well in one setting may not function so well in another.
How Does Warehouse Picking Work?
Order picking in a warehouse refers to the retrieval of goods from a storage facility or distribution center to fulfill a customer's order. Warehouse picking is a crucial part of the order fulfillment process, and it takes sophisticated machinery and labor-focused processes to guarantee a high rate of accuracy for every order that ships out of the warehouse.
4 Warehouse Picking Strategies
One of the most efficient ways to enhance the supply chain is to enhance warehouse picking procedures. One picking strategy may be better suited to your needs than others, depending on factors like the size of your warehouse, the variety of products stored there, and the number of employees you have. Learn the ins and outs of warehouse slotting so you can arrange your storage facility optimally for the picking method you intend to use.
These are four of the most common warehouse-picking strategies:
1. Discrete Order Picking
Discrete picking is a common technique because it can be easily adapted to just about any warehouse environment, especially the smaller ones. One product at a time is selected by the picker until the entire customer order has been fulfilled using this method.
Due to the time-consuming nature of manually picking each item in an order for one customer before moving on to the next customer's order, this method is best suited for smaller warehouses or those with a more limited product offering. The main advantage of this system is the simplicity with which orders can be monitored and fulfilled.
Because of this oversight, it can boost customer satisfaction, too. However, for a large warehouse with numerous SKUs and frequent orders, this procedure can be time-consuming and inefficient.
2. Zone Order Picking
Therefore, zone picking is the answer to the previously mentioned problem.
This method is straightforward; a picker takes whatever product lands in his zone and moves on. A second picker will do the same with the items that land in his area. Orders from multiple customers are fulfilled by combining products from across multiple zones, which are then sorted according to the specific needs of each customer before being packed and shipped. The term "pick and pass" is often used to describe this tactic.
The primary benefit of zone picking is that all products are separated into different zones according to their categories, and pickers are assigned to each zone individually. As a result, the picker does not have to waste time or energy running all over the massive warehouse looking for the product, and the retrieval process is streamlined. The large warehouses that stock many different SKUs will benefit greatly from this method.
3. Batch Order Picking
When a picker needs to walk a long distance to collect all of the products, batch picking is the most efficient method. In this system, a picker accepts orders from multiple customers at once and fills those orders for the same item. A picker needs to make only one trip to the designated area to retrieve the products for several different orders. This will prevent him from having to make multiple trips to the same racks to fulfill different orders.
4. Wave Order Picking
The wave picking method is an extension of the zone and batch-picking processes. Once all of the goods have been brought to the main packing desk by the pickers from their respective zones, a picker sorts the goods received from various zone pickers into orders for specific customers. After the order has been sorted, it is packaged individually for each customer.
The greatest advantage of this order is that it allows the sorter to devote a set amount of time each day to the task, which in turn reduces the amount of time and effort required to complete the task.
Picking the Right Strategy for Your Business
There are many various picking methods available, so it's natural to feel overwhelmed when deciding on one to implement in your warehouse. Each of the previous options has its own set of pros and cons, so choosing the best picking strategy for your company is essential.
Here are some things to think about as you settle on a strategy for picking:
- The first step is to determine how many orders or transactions you typically receive daily.
- Second, consider your inventory. If you divide your inventory into sections according to how quickly they sell, you can put the most popular items within easy reach.
- Find out how many products are typically made in a specific order, or if there are items commonly ordered together.
- Know your average order volume, which can help you identify the best strategy and any necessary technology to aid in the picking process.
Understanding the Importance of Warehouse Picking
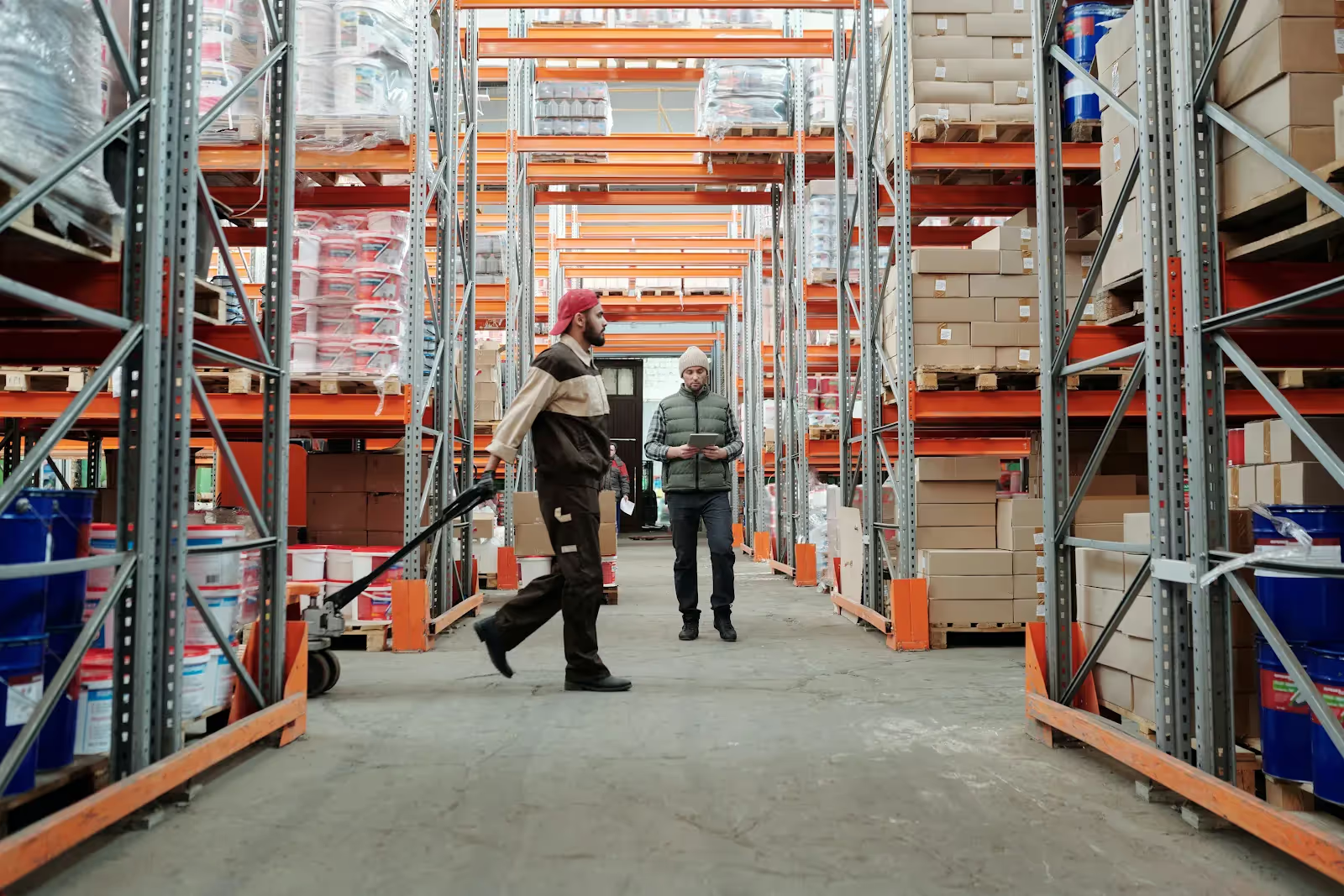
Picking orders more quickly and accurately will lead to happier customers, so it is crucial to implement the best order picking system for your warehouse. These advantages are provided by an order picking system in a warehouse:
1. Lower Warehouse Costs
Due to the time and effort required, picking in a warehouse, especially a large one, can be quite costly. To better assist your pickers in fulfilling customer orders, consider implementing a warehouse management system.
Investing in a warehouse order picking system that can assign multiple orders that are similar to a single picker will improve the accuracy and efficiency of the order picking process while also reducing costs and the amount of time spent on the task.
2. Higher Customer Satisfaction
Picking errors in the warehouse can have a significant impact on customer satisfaction if they lead to late or incorrect shipments.
And if it is taking too long to pick orders, delaying order fulfillment, some customers will not be happy about the delay or the occasional delivery exception. This is a crucial point in the logistics of online shopping and must be executed flawlessly every time.
An important KPI is your order accuracy rate, which is related to the frequency with which customers contact support, leave negative feedback, and make exchanges or returns on your online store. It can also make customers reluctant to buy from you again, cutting down on repeat business and damaging customer loyalty.
3. Ease Warehouse Staff Workload
Having the right warehouse picking system in place allows your warehouse staff to do their jobs more efficiently and accurately. With optimized routes assigned to pickers automatically, along with validations and photos to verify they are retrieving the correct items from the order, efficiency can be increased without sacrificing precision.
It is important to note that optimized warehousing (e.g., having a warehouse that is organized, utilizes space efficiently, and has items that are commonly ordered together close to each other) goes hand in hand with the right picking strategies and technology.
How Can You Make the Warehouse Picking Process More Efficient?
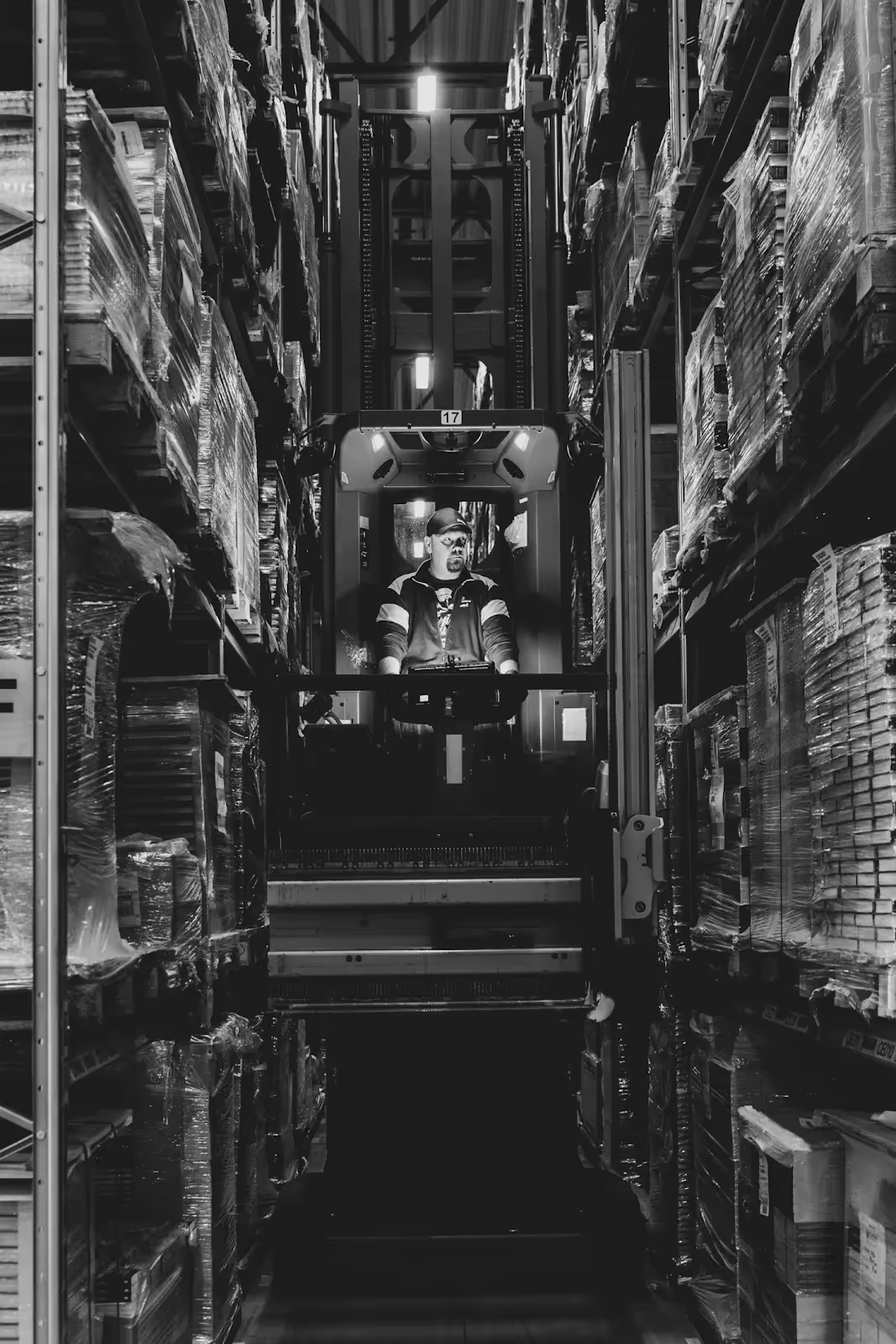
Warehouse managers should always be on the lookout for more efficient order picking techniques and know how to maximize their use. To reduce picking times, the most efficient methods prioritize easy access to the most frequently selected items. Here are some things to keep in mind to maximize warehouse picking efficiency:
1. Implement a WMS
When combined with a well-run warehouse and dedicated staff, warehouse management software can boost productivity without sacrificing precision in order fulfillment. Among the many functions a WMS should perform is the automatic generation of pick lists, the precise presentation of product availability, the provision of real-time insight into the status of orders, the prediction of when to replenish inventory via reorder point notifications, and the facilitation of staff labor planning.
2. Get the Right Equipment
To automate processes, improve worker safety, and facilitate faster, smoother traffic flow, warehouse management teams need to equip their facilities with the appropriate tools and machinery. There are always new ways and new tools to use to improve the warehouse picking process, such as forklifts to move large containers and rows of high warehouse racks to stack pallets, conveyor systems for sorting orders, barcodes and inventory scanners to improve tracking, and even wearable devices to do away with paper or bulky laptops.
3. Optimize the Warehouse Space
Because of the interconnected nature of the various order fulfillment processes, your warehouse will need constant optimization as new tools and methods are introduced and existing ones refined to facilitate smoother workflows at each stage.
4. Track Productivity in the Warehouse
You should monitor warehouse output so you can better assist your pickers and maximize efficiency. Order picking accuracy, shipping times, total units in storage, average warehouse utilization, and other distribution metrics should all be tracked and discussed regularly to ensure maximum efficiency.
5. Outsource Warehouse Picking and Order Fulfillment
When it comes to improving the picking process in the warehouse, outsourcing fulfillment is the most hands-off option. You can free up warehouse space without quickly outgrowing your current setup by outsourcing only the parts of the fulfillment process that you do not want to handle in-house (such as direct-to-consumer fulfillment) while keeping the parts that you do handle in-house (such as B2B eCommerce orders).
If you'd like to store your eCommerce inventory in a secure location while your team handles fulfillment, consider using a third-party logistics (3PL) provider like ShipNetwork.
Warehouse Picking Best Practices
Because order selection is so crucial to the success of your company, you must employ effective stock picking tactics. However, to pick orders effectively, you need to adhere to some established protocols:
Maintain a Steady Supply of Goods in Stock
Maintaining a steady supply of products is essential for efficient selection. Keep products in stock per customer demand so that they can be easily retrieved by a picker or a robot.
Put Money Into Automation and Warehouse Management Technologies
Reduce the number of people needed for the picking process by making use of automation tools like robots, AGVs, cobots, and so on. The deployment of these robots in a warehouse has many benefits, including the elimination of human mistakes and the acceleration of the fulfillment of orders.
Optimize Warehouse Layout and Logistics
Warehouse managers and facility managers should set up the warehouse such that the pickers have quick and easy access to the products they are tasked with retrieving. The key to quicker order fulfillment is arranging the warehouse layout in a way that decreases the walking time for the pickers.
Strategically Store the Best Sellers or Bundled and Kitted Items
It's helpful to store high-demand items close to the packing area, where they can be quickly and easily retrieved. It's commonly believed that the top 20% of a store's inventory accounts for 80% of the company's total sales. As a result, the remaining 80% of products can be stored more freely, giving you more options for where to keep them so that they can be quickly and easily retrieved.
Advantages of Using a 3PL for Warehouse Picking & Packing Services
A reduction in the amount of customer returns is one of the many advantages offered by working with a third-party logistics provider (3PL) for picking and packaging services. Return logistics can be expensive, therefore utilizing technology to reduce the number of errors and improve accuracy is a significant benefit.
In addition, because of the flexibility that they offer, 3PL suppliers can rapidly adapt to changes in demand while preserving the continuity of the picking and packing processes.
Working with a 3PL provider can help you save money on shipping charges, which is another advantage of using their services. Because the 3PL handles selecting and packing on your behalf, they can obtain bulk pricing by merging your items with those of other shipments.
Because ground shipping and storage expenses are becoming more inexpensive, you will be able to pass these cost savings on to your customers.
The utilization of picking and packaging services provided by a 3PL might be of particular benefit to online businesses that do not have a physical location. Because of this, the company can run with low overhead costs and doesn't have to worry about securing funding for its logistical infrastructure.
Improve Warehouse Picking Efficiency With ShipNetwork

The management of a company's supply chain is tasked with increasing customer satisfaction while simultaneously lowering operating expenses to maintain the organization's bottom line in the face of intense competition and ever-shifting consumer demand. The proactive optimization of fulfillment operations, in particular the picking activities in warehouses, is the critical factor in attaining this goal.
As a result, facility managers are obligated to select the optimal picking strategy for their particular facility, put into action the most effective picking methods, and make use of the most appropriate automation tools and equipment.
But if you have grown too large to effectively manage your warehouse, you have options. By partnering with a 3PL for order fulfillment and warehouse picking, you get access to the experts who have optimized their space and streamlined their processes.
At ShipNetwork, we can help you find the right warehouse picking strategy to improve efficiency and increase customer satisfaction. Request a Quote today to learn how we can help your company with your warehouse picking needs.
Picking is a very laborious and time-consuming part of order fulfillment. Fortunately, there are a variety of methods you may employ to improve your selection process through the strategic use of manpower and other forms of material handling technology. It's crucial to make sure you're employing the best picking approach for your company before investing in technology or automation to back up your choosing processes and cut costs.
Unfortunately, there is no universally optimal picking technique. When deciding on a warehouse picking strategy, you should think about your order profile, material flow, the physical layout of the facility, the number of line items in an order, the availability of workers, and how/when orders are released by your management system. What does well in one setting may not function so well in another.
How Does Warehouse Picking Work?
Order picking in a warehouse refers to the retrieval of goods from a storage facility or distribution center to fulfill a customer's order. Warehouse picking is a crucial part of the order fulfillment process, and it takes sophisticated machinery and labor-focused processes to guarantee a high rate of accuracy for every order that ships out of the warehouse.
4 Warehouse Picking Strategies
One of the most efficient ways to enhance the supply chain is to enhance warehouse picking procedures. One picking strategy may be better suited to your needs than others, depending on factors like the size of your warehouse, the variety of products stored there, and the number of employees you have. Learn the ins and outs of warehouse slotting so you can arrange your storage facility optimally for the picking method you intend to use.
These are four of the most common warehouse-picking strategies:
1. Discrete Order Picking
Discrete picking is a common technique because it can be easily adapted to just about any warehouse environment, especially the smaller ones. One product at a time is selected by the picker until the entire customer order has been fulfilled using this method.
Due to the time-consuming nature of manually picking each item in an order for one customer before moving on to the next customer's order, this method is best suited for smaller warehouses or those with a more limited product offering. The main advantage of this system is the simplicity with which orders can be monitored and fulfilled.
Because of this oversight, it can boost customer satisfaction, too. However, for a large warehouse with numerous SKUs and frequent orders, this procedure can be time-consuming and inefficient.
2. Zone Order Picking
Therefore, zone picking is the answer to the previously mentioned problem.
This method is straightforward; a picker takes whatever product lands in his zone and moves on. A second picker will do the same with the items that land in his area. Orders from multiple customers are fulfilled by combining products from across multiple zones, which are then sorted according to the specific needs of each customer before being packed and shipped. The term "pick and pass" is often used to describe this tactic.
The primary benefit of zone picking is that all products are separated into different zones according to their categories, and pickers are assigned to each zone individually. As a result, the picker does not have to waste time or energy running all over the massive warehouse looking for the product, and the retrieval process is streamlined. The large warehouses that stock many different SKUs will benefit greatly from this method.
3. Batch Order Picking
When a picker needs to walk a long distance to collect all of the products, batch picking is the most efficient method. In this system, a picker accepts orders from multiple customers at once and fills those orders for the same item. A picker needs to make only one trip to the designated area to retrieve the products for several different orders. This will prevent him from having to make multiple trips to the same racks to fulfill different orders.
4. Wave Order Picking
The wave picking method is an extension of the zone and batch-picking processes. Once all of the goods have been brought to the main packing desk by the pickers from their respective zones, a picker sorts the goods received from various zone pickers into orders for specific customers. After the order has been sorted, it is packaged individually for each customer.
The greatest advantage of this order is that it allows the sorter to devote a set amount of time each day to the task, which in turn reduces the amount of time and effort required to complete the task.
Picking the Right Strategy for Your Business
There are many various picking methods available, so it's natural to feel overwhelmed when deciding on one to implement in your warehouse. Each of the previous options has its own set of pros and cons, so choosing the best picking strategy for your company is essential.
Here are some things to think about as you settle on a strategy for picking:
- The first step is to determine how many orders or transactions you typically receive daily.
- Second, consider your inventory. If you divide your inventory into sections according to how quickly they sell, you can put the most popular items within easy reach.
- Find out how many products are typically made in a specific order, or if there are items commonly ordered together.
- Know your average order volume, which can help you identify the best strategy and any necessary technology to aid in the picking process.
Understanding the Importance of Warehouse Picking
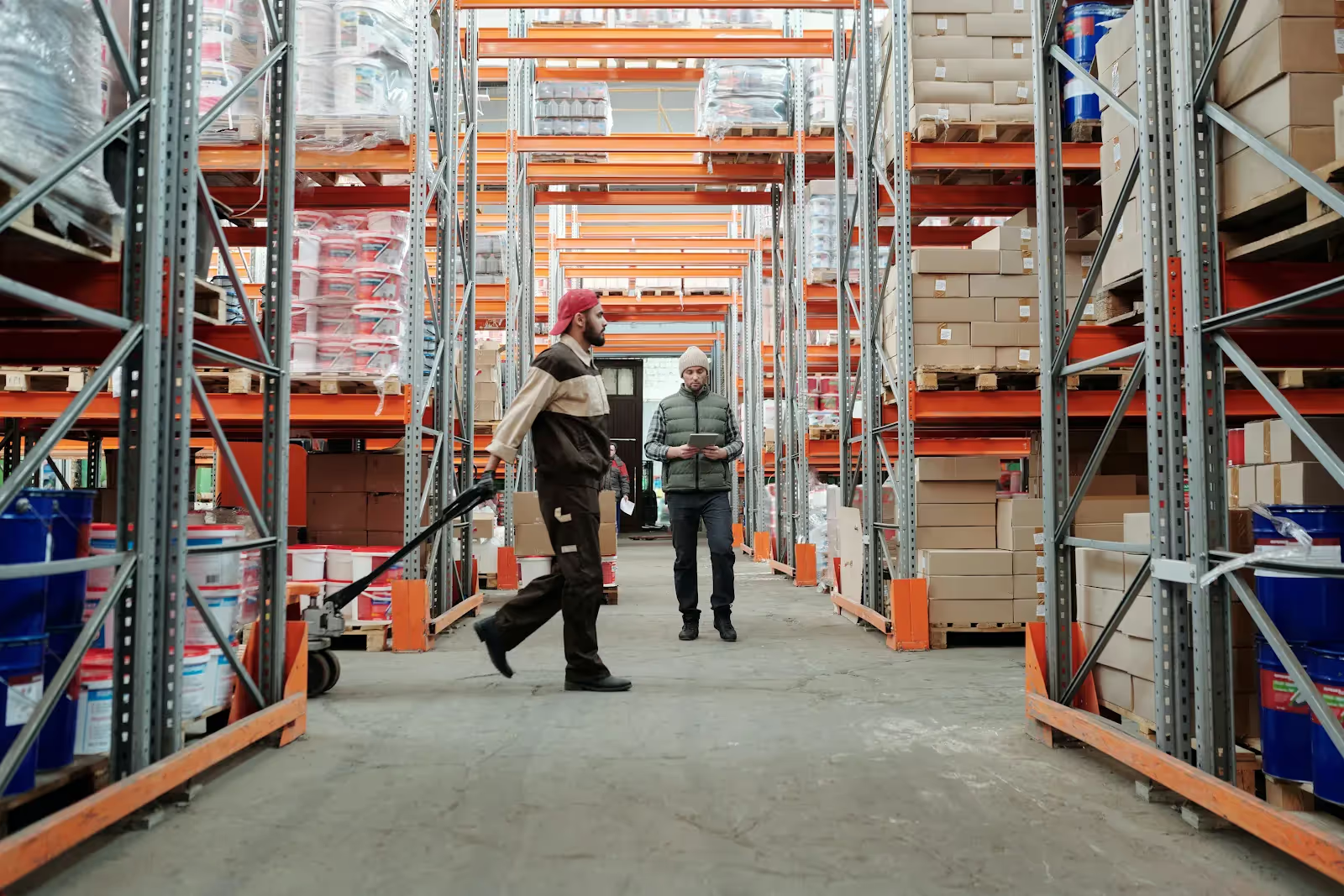
Picking orders more quickly and accurately will lead to happier customers, so it is crucial to implement the best order picking system for your warehouse. These advantages are provided by an order picking system in a warehouse:
1. Lower Warehouse Costs
Due to the time and effort required, picking in a warehouse, especially a large one, can be quite costly. To better assist your pickers in fulfilling customer orders, consider implementing a warehouse management system.
Investing in a warehouse order picking system that can assign multiple orders that are similar to a single picker will improve the accuracy and efficiency of the order picking process while also reducing costs and the amount of time spent on the task.
2. Higher Customer Satisfaction
Picking errors in the warehouse can have a significant impact on customer satisfaction if they lead to late or incorrect shipments.
And if it is taking too long to pick orders, delaying order fulfillment, some customers will not be happy about the delay or the occasional delivery exception. This is a crucial point in the logistics of online shopping and must be executed flawlessly every time.
An important KPI is your order accuracy rate, which is related to the frequency with which customers contact support, leave negative feedback, and make exchanges or returns on your online store. It can also make customers reluctant to buy from you again, cutting down on repeat business and damaging customer loyalty.
3. Ease Warehouse Staff Workload
Having the right warehouse picking system in place allows your warehouse staff to do their jobs more efficiently and accurately. With optimized routes assigned to pickers automatically, along with validations and photos to verify they are retrieving the correct items from the order, efficiency can be increased without sacrificing precision.
It is important to note that optimized warehousing (e.g., having a warehouse that is organized, utilizes space efficiently, and has items that are commonly ordered together close to each other) goes hand in hand with the right picking strategies and technology.
How Can You Make the Warehouse Picking Process More Efficient?
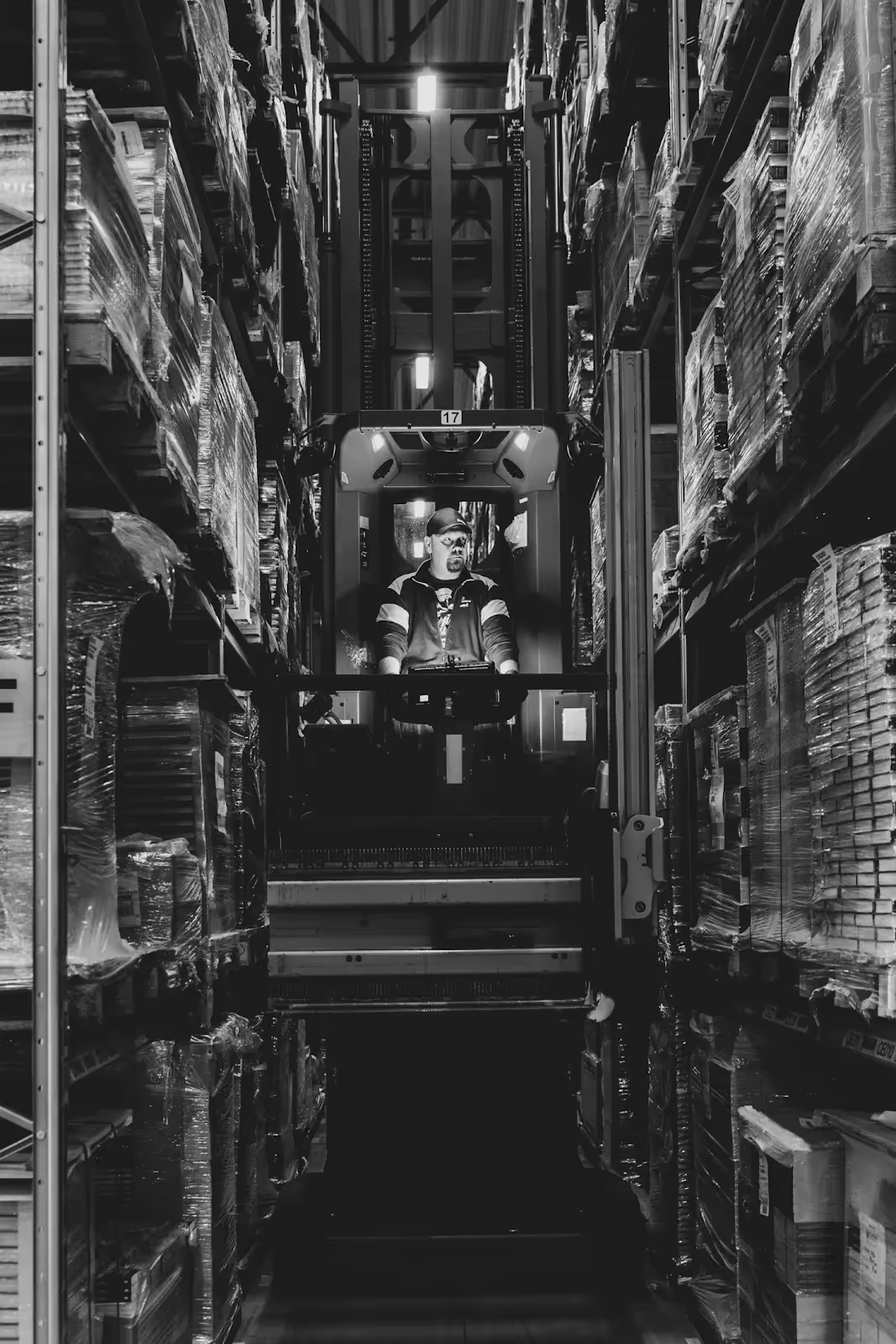
Warehouse managers should always be on the lookout for more efficient order picking techniques and know how to maximize their use. To reduce picking times, the most efficient methods prioritize easy access to the most frequently selected items. Here are some things to keep in mind to maximize warehouse picking efficiency:
1. Implement a WMS
When combined with a well-run warehouse and dedicated staff, warehouse management software can boost productivity without sacrificing precision in order fulfillment. Among the many functions a WMS should perform is the automatic generation of pick lists, the precise presentation of product availability, the provision of real-time insight into the status of orders, the prediction of when to replenish inventory via reorder point notifications, and the facilitation of staff labor planning.
2. Get the Right Equipment
To automate processes, improve worker safety, and facilitate faster, smoother traffic flow, warehouse management teams need to equip their facilities with the appropriate tools and machinery. There are always new ways and new tools to use to improve the warehouse picking process, such as forklifts to move large containers and rows of high warehouse racks to stack pallets, conveyor systems for sorting orders, barcodes and inventory scanners to improve tracking, and even wearable devices to do away with paper or bulky laptops.
3. Optimize the Warehouse Space
Because of the interconnected nature of the various order fulfillment processes, your warehouse will need constant optimization as new tools and methods are introduced and existing ones refined to facilitate smoother workflows at each stage.
4. Track Productivity in the Warehouse
You should monitor warehouse output so you can better assist your pickers and maximize efficiency. Order picking accuracy, shipping times, total units in storage, average warehouse utilization, and other distribution metrics should all be tracked and discussed regularly to ensure maximum efficiency.
5. Outsource Warehouse Picking and Order Fulfillment
When it comes to improving the picking process in the warehouse, outsourcing fulfillment is the most hands-off option. You can free up warehouse space without quickly outgrowing your current setup by outsourcing only the parts of the fulfillment process that you do not want to handle in-house (such as direct-to-consumer fulfillment) while keeping the parts that you do handle in-house (such as B2B eCommerce orders).
If you'd like to store your eCommerce inventory in a secure location while your team handles fulfillment, consider using a third-party logistics (3PL) provider like ShipNetwork.
Warehouse Picking Best Practices
Because order selection is so crucial to the success of your company, you must employ effective stock picking tactics. However, to pick orders effectively, you need to adhere to some established protocols:
Maintain a Steady Supply of Goods in Stock
Maintaining a steady supply of products is essential for efficient selection. Keep products in stock per customer demand so that they can be easily retrieved by a picker or a robot.
Put Money Into Automation and Warehouse Management Technologies
Reduce the number of people needed for the picking process by making use of automation tools like robots, AGVs, cobots, and so on. The deployment of these robots in a warehouse has many benefits, including the elimination of human mistakes and the acceleration of the fulfillment of orders.
Optimize Warehouse Layout and Logistics
Warehouse managers and facility managers should set up the warehouse such that the pickers have quick and easy access to the products they are tasked with retrieving. The key to quicker order fulfillment is arranging the warehouse layout in a way that decreases the walking time for the pickers.
Strategically Store the Best Sellers or Bundled and Kitted Items
It's helpful to store high-demand items close to the packing area, where they can be quickly and easily retrieved. It's commonly believed that the top 20% of a store's inventory accounts for 80% of the company's total sales. As a result, the remaining 80% of products can be stored more freely, giving you more options for where to keep them so that they can be quickly and easily retrieved.
Advantages of Using a 3PL for Warehouse Picking & Packing Services
A reduction in the amount of customer returns is one of the many advantages offered by working with a third-party logistics provider (3PL) for picking and packaging services. Return logistics can be expensive, therefore utilizing technology to reduce the number of errors and improve accuracy is a significant benefit.
In addition, because of the flexibility that they offer, 3PL suppliers can rapidly adapt to changes in demand while preserving the continuity of the picking and packing processes.
Working with a 3PL provider can help you save money on shipping charges, which is another advantage of using their services. Because the 3PL handles selecting and packing on your behalf, they can obtain bulk pricing by merging your items with those of other shipments.
Because ground shipping and storage expenses are becoming more inexpensive, you will be able to pass these cost savings on to your customers.
The utilization of picking and packaging services provided by a 3PL might be of particular benefit to online businesses that do not have a physical location. Because of this, the company can run with low overhead costs and doesn't have to worry about securing funding for its logistical infrastructure.
Improve Warehouse Picking Efficiency With ShipNetwork

The management of a company's supply chain is tasked with increasing customer satisfaction while simultaneously lowering operating expenses to maintain the organization's bottom line in the face of intense competition and ever-shifting consumer demand. The proactive optimization of fulfillment operations, in particular the picking activities in warehouses, is the critical factor in attaining this goal.
As a result, facility managers are obligated to select the optimal picking strategy for their particular facility, put into action the most effective picking methods, and make use of the most appropriate automation tools and equipment.
But if you have grown too large to effectively manage your warehouse, you have options. By partnering with a 3PL for order fulfillment and warehouse picking, you get access to the experts who have optimized their space and streamlined their processes.
At ShipNetwork, we can help you find the right warehouse picking strategy to improve efficiency and increase customer satisfaction. Request a Quote today to learn how we can help your company with your warehouse picking needs.