The sharing of business information is the only way that any logistical task can get done. When you are moving goods from one place to the next, you need to have the right information in the right hands. Fortunately, the industry has worked to standardize the information that is used for many of these purposes with electronic data interchange, or EDI transaction codes.
Let’s take a look at what EDI codes are and how they can improve your business operations when you work with a 3PL, shipping carrier, or other logistics partner.
What Are EDI Codes?
Electronic data interchange (EDI) codes were developed to be standardized and to be indifferent to the communications methods used by businesses and the software technology used to transmit and receive EDI data.
When one company needs to place an order with another, for example, they will use EDI transactions, which are standardized electronic business documents used by trading partners to send and receive business information. EDI standards are used for the electronic exchange of documents like purchase orders, invoices, acknowledgments, payments, and tracking information between businesses and their trading partners.
Many different EDI transaction codes correspond to different pieces of information on various types of business documents like invoices and purchase orders. EDI allows for the secure and efficient transfer of these documents between businesses. A transaction set is a collection of related pieces of information that must appear in a predetermined order and format within a single document. By maintaining a consistent order and format, the receiving computer system can readily determine which component stands for the sender's company name, which represents the invoice number, and so on.
There is required information that must be included in every EDI transaction document. Noncompliance with these standards renders an EDI document useless. By strictly following EDI feed formatting rules, you can specify where and how each piece of data on the document will be accessed. One of the many transaction numbers available in the EDI public format is used to identify each document.
What Is in an EDI Document?
Data elements, segments, and envelopes in an EDI document are all structured per the rules of a specific EDI standard. A purchase order or other EDI document must be formatted exactly as specified by the applicable standard. These guidelines specify the specific locations and access points for all of the information contained in the document. This ensures that the EDI translator on the receiving computer can easily locate the buyer's company name, PO number, items being ordered, prices for each item, etc. in an incoming EDI purchase order. The data will then be automatically fed into the receiver's order entry system in the correct internal format.
Taking a step back, we can see that there are three distinct parts to every transaction set: Information is broken down into smaller pieces, or "data elements," that make up the whole. Each data element within a transaction set is defined by an EDI standard, including its data type (numeric, alphanumeric, date/time), minimum and maximum allowable length, and "code values" (like a currency code element for prices).
For example, in an EDI 850 Purchase Order, the item number, quantity, units, and price are all segments related to the same item. Segment IDs are unique identifiers that reveal the segment's data element types at the very beginning of the segment. A data element separator (an asterisk by default in the ANSI X12 EDI standard) delimits individual data elements within the segment.
There are required and optional parts, as well as parts that depend on others being present. This information, including the order in which segments and elements must be transmitted and whether or not a segment may be repeated, is defined by the EDI standard in use. A transaction set is a collection of matching parts in the correct order. EDI transaction sets are sent encased in envelopes for security and convenience.
What Are EDI Envelopes?
The three "envelopes" used in EDI document transmission are the "Message" envelope, the "Group" envelope, and the "Interchange" envelope. EDI documents are exchanged using multiple envelopes, similar to how paper business documents are sent in envelopes and multiple documents can be mailed in a single envelope.
A separate envelope is used for each set of transactions. A group envelope is used to store multiple related transaction sets (such as purchase orders) together. The group envelope is required by ANSI but not EDIFACT.
What Are Transactions in EDI?
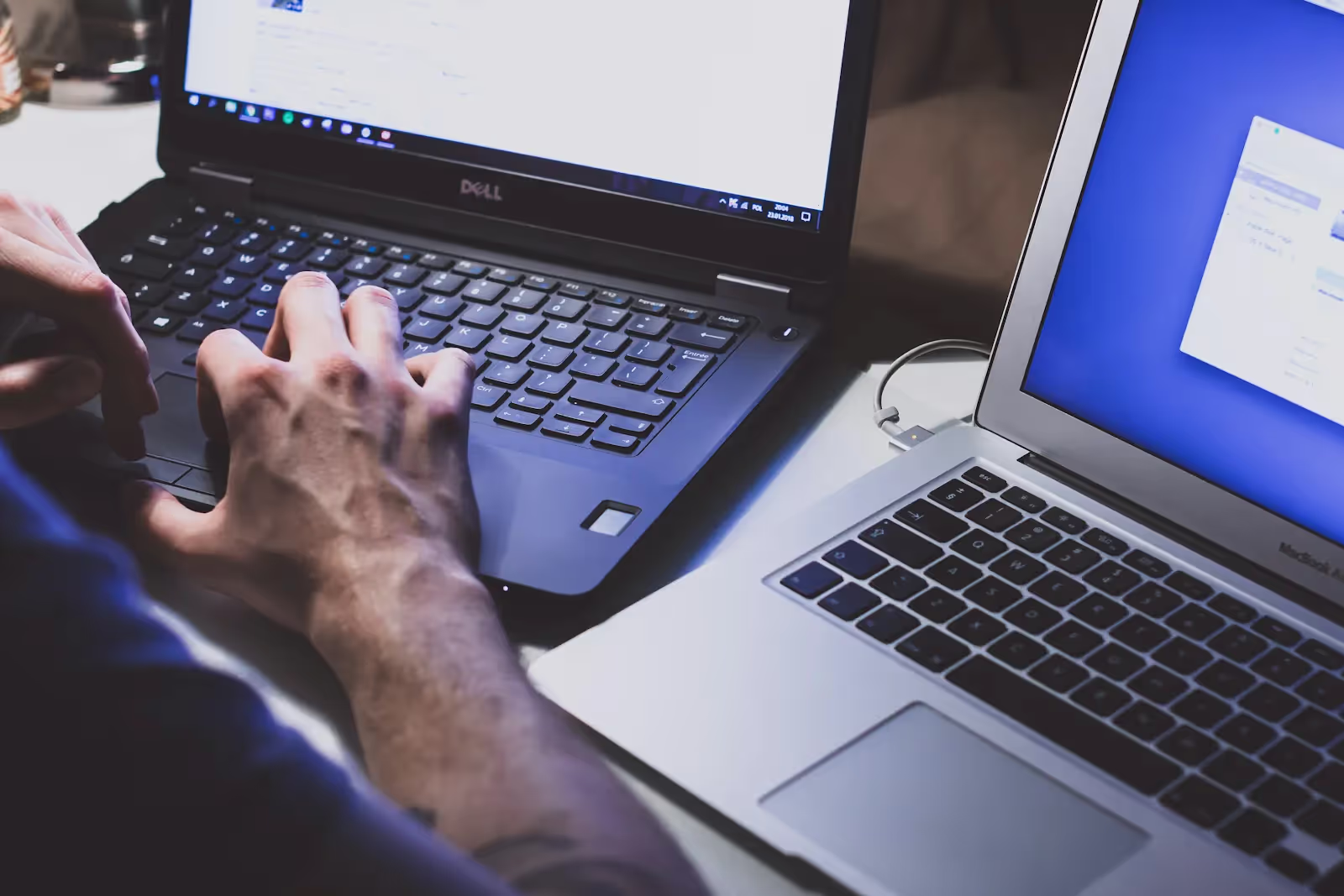
EDI transactions are essential for conducting business with many of the world's largest corporations. These are seven of the most common EDI codes that are used when working with companies like Walmart, Amazon, FedEx, and others:
- EDI 856: Ship Notice/Manifest
- EDI 810: Invoice
- EDI 850: Purchase Order
- EDI 855: Purchase Order Acknowledgment
- EDI 820: Payment Order/Remittance Advice
- EDI 997: Functional Acknowledgment
- EDI 940: Warehouse Shipping Order
However, there are hundreds of different types of EDI transactions, so businesses adhere to established EDI standards to guarantee compatibility when exchanging data with partners in other industries.
What Is the Difference Between EDI 810 & 210?
EDI 810 is for general invoices, while EDI 210 is for motor carrier freight details and invoices. Standard invoice details are included in the EDI 810 e-transaction types, including:
- Invoice number
- Date
- Payment amount
- Buyer and seller
- Product quantity and line item pricing.
- Taxes, fees, and other charges.
- Credits or allowances
- Payment terms (due date and method)
EDI 210 information is sent from the carrier to the shipper, consignee, or third-party payment center, including these details:
- Invoice date and number.
- Bill-to information
- Order information details (items, quantities, and weights)
- Shipping methods and descriptions.
- Shipper name and address information.
- Consignee name and address information.
- Payment terms
- Delivery information (proof of delivery, tracking numbers, etc.)
What Are 850 EDI Codes?
The purchase order, which uses the official ANSI EDI code 850 e, is typically one of the first EDI transmissions sent by a company. Whether you're making a one-time purchase or setting up automatic renewals, this is the first thing you should do. The following are examples of what can be found on a purchase order:
- Purchase order number
- Order date, shipping date, and/or delivery date.
- Buyer name, address, and billing information.
- Supplier name, address, and contact information.
- Shipping method
- Product information (SKUs, UPCs, etc.)
- Product quantity and line item pricing.
- Terms of payment
Why EDI Transaction Codes Are Important
Concerns about EDI's strict adherence to standards have been raised by many in the tech industry. However, this same standardization is what has allowed EDI to endure for so long and become embedded in business practice. Without standardization, it's hard to keep B2B data exchanges running smoothly and expand them.
To some extent, APIs have not been able to replace EDI for B2B-type data exchanges because there are no true EDI standards that dictate a universal format. Given the flexibility of APIs, developers have a lot of options for how to best meet the needs of their company. Such comprehensive business rules typically do not scale well within businesses. However, the hundreds of unique EDI transaction codes are what truly unify the business language.
What Is 3PL EDI?
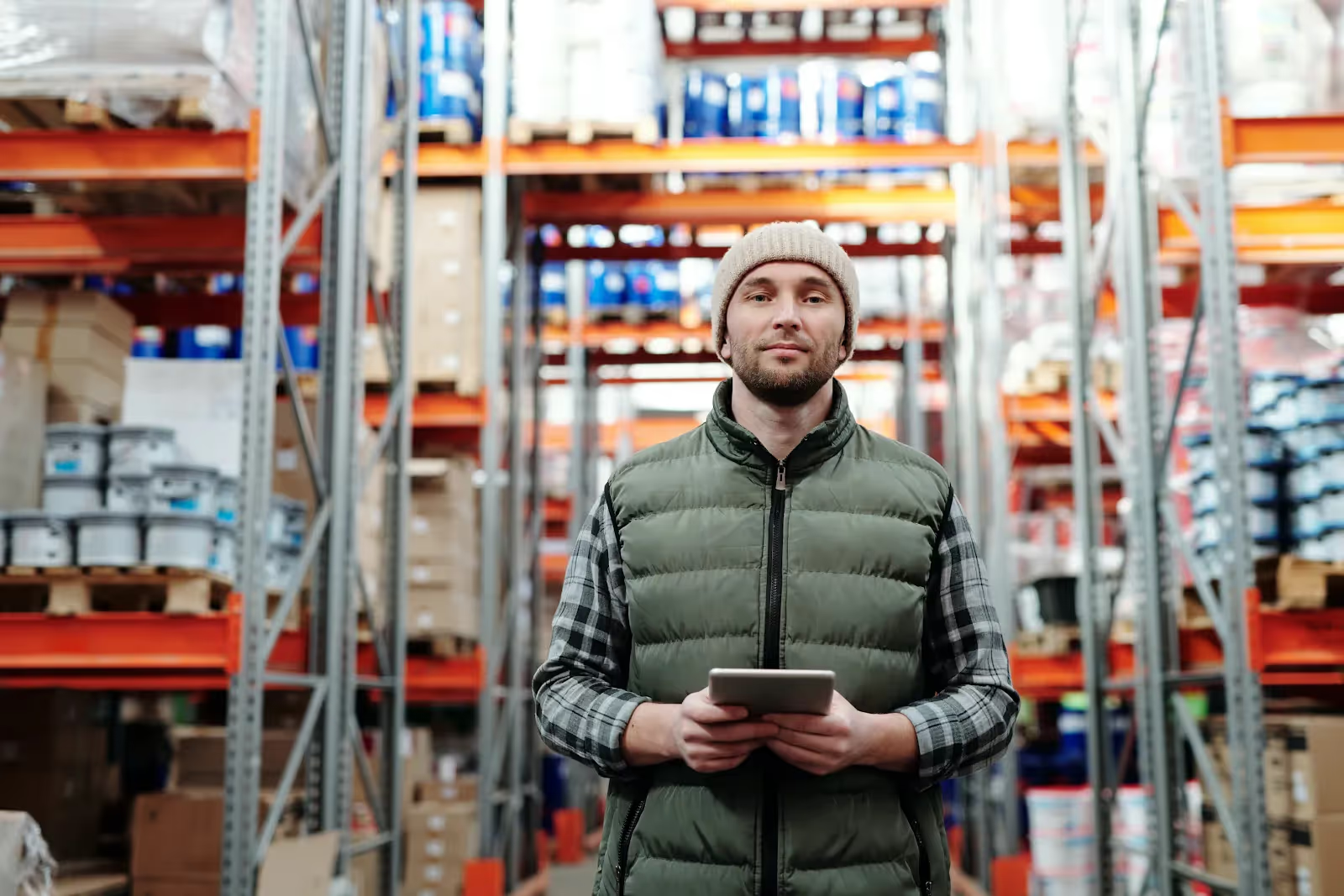
Third-party logistics electronic data interchange, or 3PL EDI, refers to the electronic transfer of business documents between 3PLs and their retailers and wholesalers. Supply chain documentation may include purchase orders, invoices, and shipping notifications, among other types of paperwork.
Since there is no longer any need for entering data manually, accuracy and reliability are both increased. This has the potential to reduce supply chain errors and shorten the time it takes to process orders. As a result, operational expenses are reduced and productivity is increased.
How EDI Helps 3PLs Improve Business Processes
Many businesses rely on EDI to efficiently and consistently exchange digital versions of business documents. EDI eliminates the need for intermediary services like the post office, fax machines, and email by establishing a direct link to back-end company databases like those used for e-commerce and ERP. Documents such as purchase orders, invoices, and advanced shipping notices are the most frequently exchanged business documents transmitted via EDI.
Companies in the logistics industry that adopt EDI see a reduction in overhead, an improvement in speed and agility, and the elimination of manual processes that are prone to error and slow down the workflow. 3PLs must have dependable automated order processing and inventory management capabilities because many businesses demand EDI compliance from all participants in their digital ecosystem. EDI systems provide that and more. EDI management is often outsourced by supply chain companies so that they can concentrate on core competencies.
3PLs use EDI to facilitate two-way communication with their clients, thereby facilitating the automation of order processing and the improvement of supply chain predictability and accuracy. With the help of EDI, businesses can grow in a scalable, cost-effective, and straightforward manner.
The Importance of EDI in 3PLs
Large logistics firms and 3PLs typically have to send anywhere from several hundred to thousands of documents every day. Processing this amount of information manually via snail mail, messenger service, fax machine, computer, or telephone would be a time-consuming and expensive endeavor that is prone to error.
Therefore, 3PL providers and their customers utilize EDI to communicate and share data such as orders, deliveries, shipments, balances, reports, etc. 3PLs and product suppliers commonly adopt EDI to automate their data exchange processes. By doing so, the need for manual data entry into an accounting or business system by business partners is eliminated. EDI messages are sent instantly and free from human error.
If you need to share information with a 3PL provider, EDI is your best bet. In terms of efficiency, safety, and cost, this method of business communication cannot be surpassed. If you're working with a 3PL, they'll need to know specifics like where the packages will be delivered, when they'll be shipped, how many of each item you're sending, what size boxes they'll be shipped in, etc.
The manufacturer must know how much of a product is in stock, where it is going, how much is being written off, and which stores are getting what quantities. Without accurate data, businesses risk running out of stock, suffering financial losses, and wasting time and energy dealing with issues like late or incorrect deliveries, lengthy approval processes, and frequent account adjustments.
Common EDI Codes for 3PLs
3PL providers use a variety of EDI documents to exchange information with their customers, suppliers, carriers, and other partners. Some of the commonly used EDI documents in 3PL include:
- 850 Purchase Order: Transmits a purchase order from a customer to a 3PL provider, and includes item description, quantity, and price.
- 855 Purchase Order Acknowledgement: Used by the 3PL to acknowledge the receipt of goods.
- 856 Advance Shipment Notice: Informs the customer of the expected delivery date and time.
- 940 Warehouse Shipping Order: Used by the 3PL to notify a warehouse of an upcoming shipment.
- 945 Warehouse Shipping Advice: Used by the warehouse to notify the 3PL that the shipment was shipped.
- 944 Warehouse Stock Transfer Receipt Advice: Helps the warehouse notify the 3PL that a stock transfer was received.
- 997 Functional Acknowledgment: Acknowledges the receipt of an EDI document by the recipient.
- 810 Invoice: Provides the customer with an electronic invoice for services rendered, and it includes the billing period, charges, and payment due date.
The use of these EDI documents allows 3PLs to streamline their order, inventory, and delivery processes through the use of automation. These factors also contribute to a decrease in miscommunication and an increase in efficiency between the 3PL and its partners.
These messages could be used with either the UN/EDIFACT standard (more common in Europe) or the ANSI X12 standard (more common in North America). Though the messages in both standards serve a similar purpose, they look different.
Leverage EDI Transaction Codes for Efficient Logistics With ShipNetwork
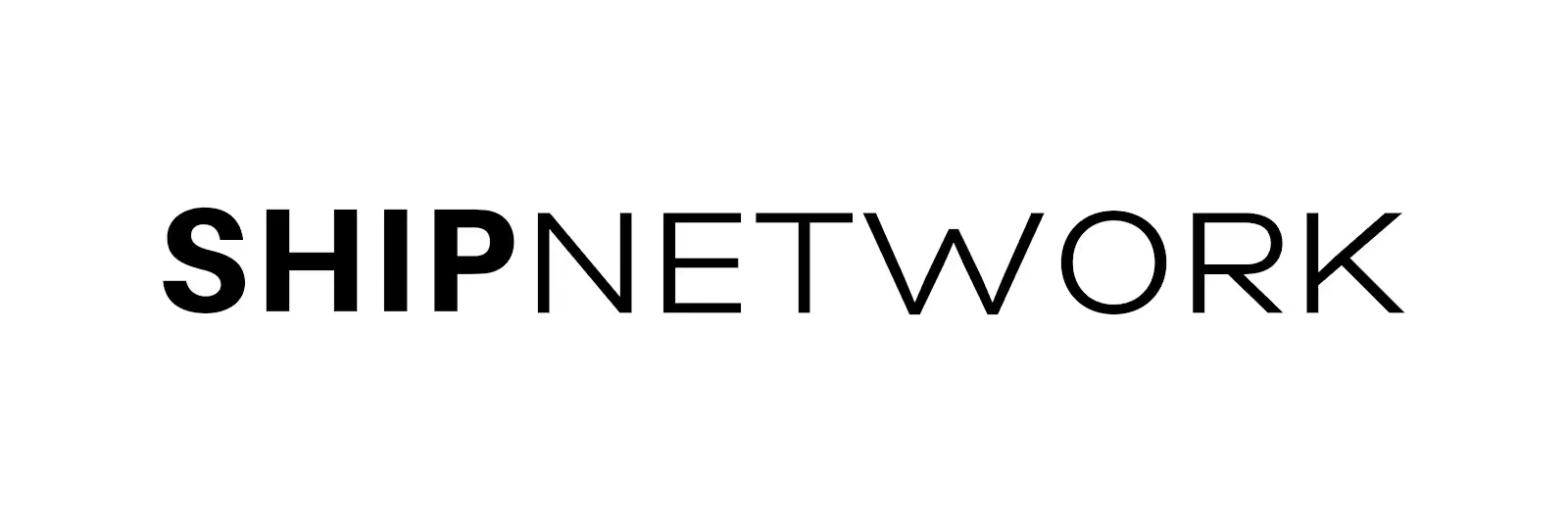
Delivering a problem-free shopping experience to customers is the top priority for any online retailer. However, even the most well-organized retail outlets sometimes have trouble promptly and accurately filling customer orders. You can streamline your logistics management with the help of ShipNetwork's knowledge of EDI codes for 3PLs and warehousing.
You can now easily send information about orders, shipments, and data with the help of EDI transaction codes that are commonly used across the industry. Additionally, you can easily track your shipping operations and view real-time analytics with the help of ShipNetwork’s user-friendly dashboard.
Reduce errors and streamline logistic operations for eCommerce by using the right EDI codes and sending the necessary info with ShipNetwork’s experts. Contact Us today to learn more.
The sharing of business information is the only way that any logistical task can get done. When you are moving goods from one place to the next, you need to have the right information in the right hands. Fortunately, the industry has worked to standardize the information that is used for many of these purposes with electronic data interchange, or EDI transaction codes.
Let’s take a look at what EDI codes are and how they can improve your business operations when you work with a 3PL, shipping carrier, or other logistics partner.
What Are EDI Codes?
Electronic data interchange (EDI) codes were developed to be standardized and to be indifferent to the communications methods used by businesses and the software technology used to transmit and receive EDI data.
When one company needs to place an order with another, for example, they will use EDI transactions, which are standardized electronic business documents used by trading partners to send and receive business information. EDI standards are used for the electronic exchange of documents like purchase orders, invoices, acknowledgments, payments, and tracking information between businesses and their trading partners.
Many different EDI transaction codes correspond to different pieces of information on various types of business documents like invoices and purchase orders. EDI allows for the secure and efficient transfer of these documents between businesses. A transaction set is a collection of related pieces of information that must appear in a predetermined order and format within a single document. By maintaining a consistent order and format, the receiving computer system can readily determine which component stands for the sender's company name, which represents the invoice number, and so on.
There is required information that must be included in every EDI transaction document. Noncompliance with these standards renders an EDI document useless. By strictly following EDI feed formatting rules, you can specify where and how each piece of data on the document will be accessed. One of the many transaction numbers available in the EDI public format is used to identify each document.
What Is in an EDI Document?
Data elements, segments, and envelopes in an EDI document are all structured per the rules of a specific EDI standard. A purchase order or other EDI document must be formatted exactly as specified by the applicable standard. These guidelines specify the specific locations and access points for all of the information contained in the document. This ensures that the EDI translator on the receiving computer can easily locate the buyer's company name, PO number, items being ordered, prices for each item, etc. in an incoming EDI purchase order. The data will then be automatically fed into the receiver's order entry system in the correct internal format.
Taking a step back, we can see that there are three distinct parts to every transaction set: Information is broken down into smaller pieces, or "data elements," that make up the whole. Each data element within a transaction set is defined by an EDI standard, including its data type (numeric, alphanumeric, date/time), minimum and maximum allowable length, and "code values" (like a currency code element for prices).
For example, in an EDI 850 Purchase Order, the item number, quantity, units, and price are all segments related to the same item. Segment IDs are unique identifiers that reveal the segment's data element types at the very beginning of the segment. A data element separator (an asterisk by default in the ANSI X12 EDI standard) delimits individual data elements within the segment.
There are required and optional parts, as well as parts that depend on others being present. This information, including the order in which segments and elements must be transmitted and whether or not a segment may be repeated, is defined by the EDI standard in use. A transaction set is a collection of matching parts in the correct order. EDI transaction sets are sent encased in envelopes for security and convenience.
What Are EDI Envelopes?
The three "envelopes" used in EDI document transmission are the "Message" envelope, the "Group" envelope, and the "Interchange" envelope. EDI documents are exchanged using multiple envelopes, similar to how paper business documents are sent in envelopes and multiple documents can be mailed in a single envelope.
A separate envelope is used for each set of transactions. A group envelope is used to store multiple related transaction sets (such as purchase orders) together. The group envelope is required by ANSI but not EDIFACT.
What Are Transactions in EDI?
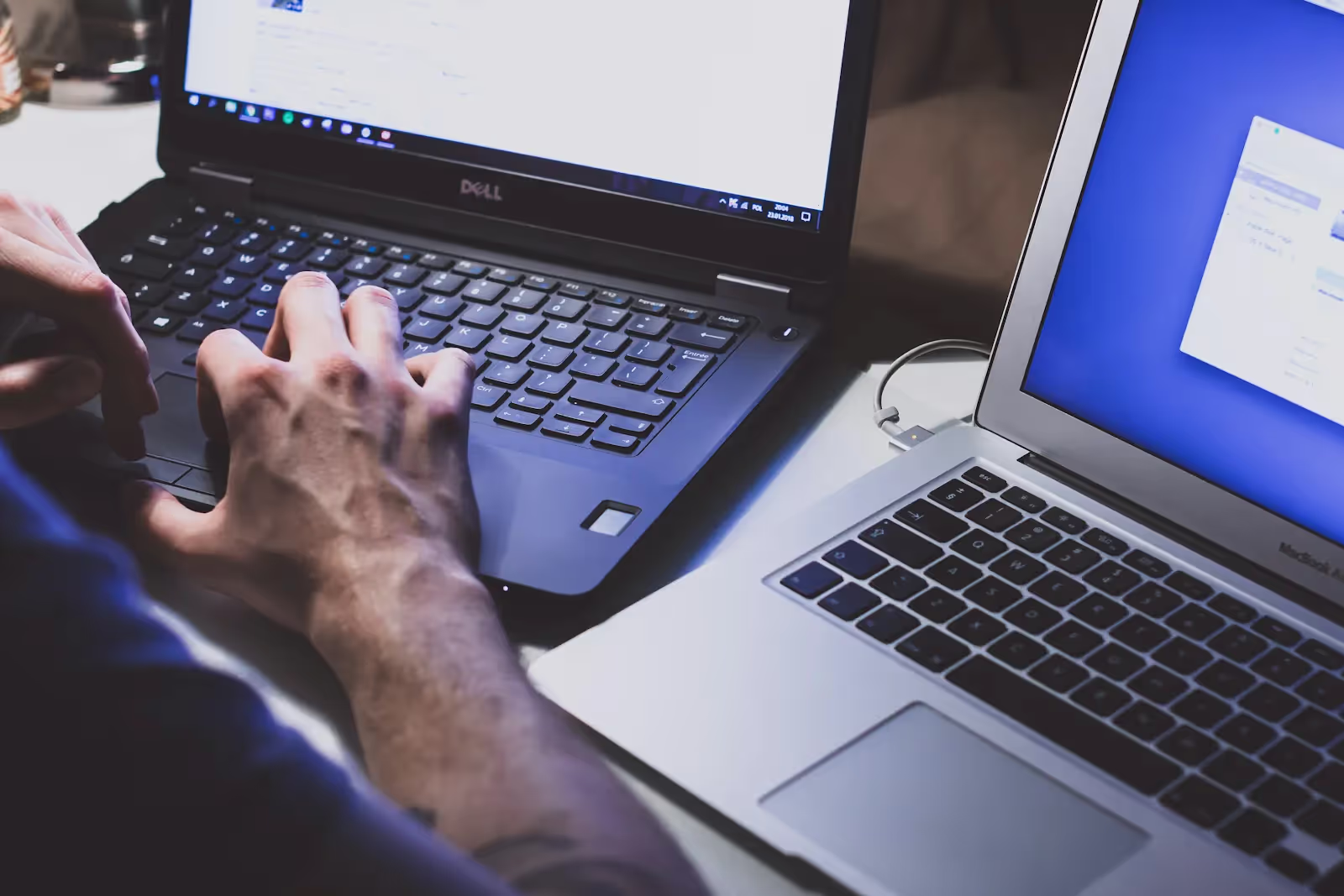
EDI transactions are essential for conducting business with many of the world's largest corporations. These are seven of the most common EDI codes that are used when working with companies like Walmart, Amazon, FedEx, and others:
- EDI 856: Ship Notice/Manifest
- EDI 810: Invoice
- EDI 850: Purchase Order
- EDI 855: Purchase Order Acknowledgment
- EDI 820: Payment Order/Remittance Advice
- EDI 997: Functional Acknowledgment
- EDI 940: Warehouse Shipping Order
However, there are hundreds of different types of EDI transactions, so businesses adhere to established EDI standards to guarantee compatibility when exchanging data with partners in other industries.
What Is the Difference Between EDI 810 & 210?
EDI 810 is for general invoices, while EDI 210 is for motor carrier freight details and invoices. Standard invoice details are included in the EDI 810 e-transaction types, including:
- Invoice number
- Date
- Payment amount
- Buyer and seller
- Product quantity and line item pricing.
- Taxes, fees, and other charges.
- Credits or allowances
- Payment terms (due date and method)
EDI 210 information is sent from the carrier to the shipper, consignee, or third-party payment center, including these details:
- Invoice date and number.
- Bill-to information
- Order information details (items, quantities, and weights)
- Shipping methods and descriptions.
- Shipper name and address information.
- Consignee name and address information.
- Payment terms
- Delivery information (proof of delivery, tracking numbers, etc.)
What Are 850 EDI Codes?
The purchase order, which uses the official ANSI EDI code 850 e, is typically one of the first EDI transmissions sent by a company. Whether you're making a one-time purchase or setting up automatic renewals, this is the first thing you should do. The following are examples of what can be found on a purchase order:
- Purchase order number
- Order date, shipping date, and/or delivery date.
- Buyer name, address, and billing information.
- Supplier name, address, and contact information.
- Shipping method
- Product information (SKUs, UPCs, etc.)
- Product quantity and line item pricing.
- Terms of payment
Why EDI Transaction Codes Are Important
Concerns about EDI's strict adherence to standards have been raised by many in the tech industry. However, this same standardization is what has allowed EDI to endure for so long and become embedded in business practice. Without standardization, it's hard to keep B2B data exchanges running smoothly and expand them.
To some extent, APIs have not been able to replace EDI for B2B-type data exchanges because there are no true EDI standards that dictate a universal format. Given the flexibility of APIs, developers have a lot of options for how to best meet the needs of their company. Such comprehensive business rules typically do not scale well within businesses. However, the hundreds of unique EDI transaction codes are what truly unify the business language.
What Is 3PL EDI?
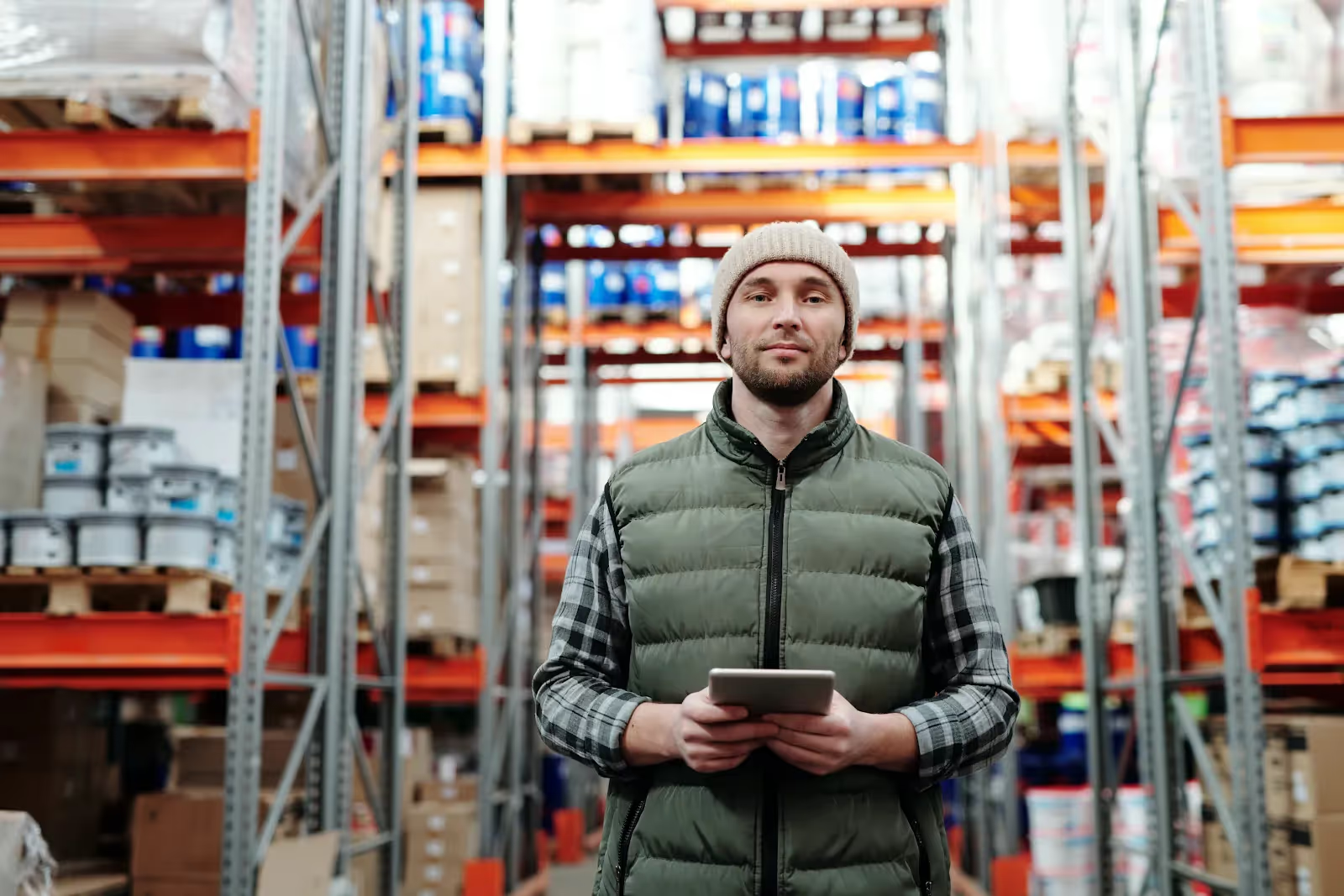
Third-party logistics electronic data interchange, or 3PL EDI, refers to the electronic transfer of business documents between 3PLs and their retailers and wholesalers. Supply chain documentation may include purchase orders, invoices, and shipping notifications, among other types of paperwork.
Since there is no longer any need for entering data manually, accuracy and reliability are both increased. This has the potential to reduce supply chain errors and shorten the time it takes to process orders. As a result, operational expenses are reduced and productivity is increased.
How EDI Helps 3PLs Improve Business Processes
Many businesses rely on EDI to efficiently and consistently exchange digital versions of business documents. EDI eliminates the need for intermediary services like the post office, fax machines, and email by establishing a direct link to back-end company databases like those used for e-commerce and ERP. Documents such as purchase orders, invoices, and advanced shipping notices are the most frequently exchanged business documents transmitted via EDI.
Companies in the logistics industry that adopt EDI see a reduction in overhead, an improvement in speed and agility, and the elimination of manual processes that are prone to error and slow down the workflow. 3PLs must have dependable automated order processing and inventory management capabilities because many businesses demand EDI compliance from all participants in their digital ecosystem. EDI systems provide that and more. EDI management is often outsourced by supply chain companies so that they can concentrate on core competencies.
3PLs use EDI to facilitate two-way communication with their clients, thereby facilitating the automation of order processing and the improvement of supply chain predictability and accuracy. With the help of EDI, businesses can grow in a scalable, cost-effective, and straightforward manner.
The Importance of EDI in 3PLs
Large logistics firms and 3PLs typically have to send anywhere from several hundred to thousands of documents every day. Processing this amount of information manually via snail mail, messenger service, fax machine, computer, or telephone would be a time-consuming and expensive endeavor that is prone to error.
Therefore, 3PL providers and their customers utilize EDI to communicate and share data such as orders, deliveries, shipments, balances, reports, etc. 3PLs and product suppliers commonly adopt EDI to automate their data exchange processes. By doing so, the need for manual data entry into an accounting or business system by business partners is eliminated. EDI messages are sent instantly and free from human error.
If you need to share information with a 3PL provider, EDI is your best bet. In terms of efficiency, safety, and cost, this method of business communication cannot be surpassed. If you're working with a 3PL, they'll need to know specifics like where the packages will be delivered, when they'll be shipped, how many of each item you're sending, what size boxes they'll be shipped in, etc.
The manufacturer must know how much of a product is in stock, where it is going, how much is being written off, and which stores are getting what quantities. Without accurate data, businesses risk running out of stock, suffering financial losses, and wasting time and energy dealing with issues like late or incorrect deliveries, lengthy approval processes, and frequent account adjustments.
Common EDI Codes for 3PLs
3PL providers use a variety of EDI documents to exchange information with their customers, suppliers, carriers, and other partners. Some of the commonly used EDI documents in 3PL include:
- 850 Purchase Order: Transmits a purchase order from a customer to a 3PL provider, and includes item description, quantity, and price.
- 855 Purchase Order Acknowledgement: Used by the 3PL to acknowledge the receipt of goods.
- 856 Advance Shipment Notice: Informs the customer of the expected delivery date and time.
- 940 Warehouse Shipping Order: Used by the 3PL to notify a warehouse of an upcoming shipment.
- 945 Warehouse Shipping Advice: Used by the warehouse to notify the 3PL that the shipment was shipped.
- 944 Warehouse Stock Transfer Receipt Advice: Helps the warehouse notify the 3PL that a stock transfer was received.
- 997 Functional Acknowledgment: Acknowledges the receipt of an EDI document by the recipient.
- 810 Invoice: Provides the customer with an electronic invoice for services rendered, and it includes the billing period, charges, and payment due date.
The use of these EDI documents allows 3PLs to streamline their order, inventory, and delivery processes through the use of automation. These factors also contribute to a decrease in miscommunication and an increase in efficiency between the 3PL and its partners.
These messages could be used with either the UN/EDIFACT standard (more common in Europe) or the ANSI X12 standard (more common in North America). Though the messages in both standards serve a similar purpose, they look different.
Leverage EDI Transaction Codes for Efficient Logistics With ShipNetwork
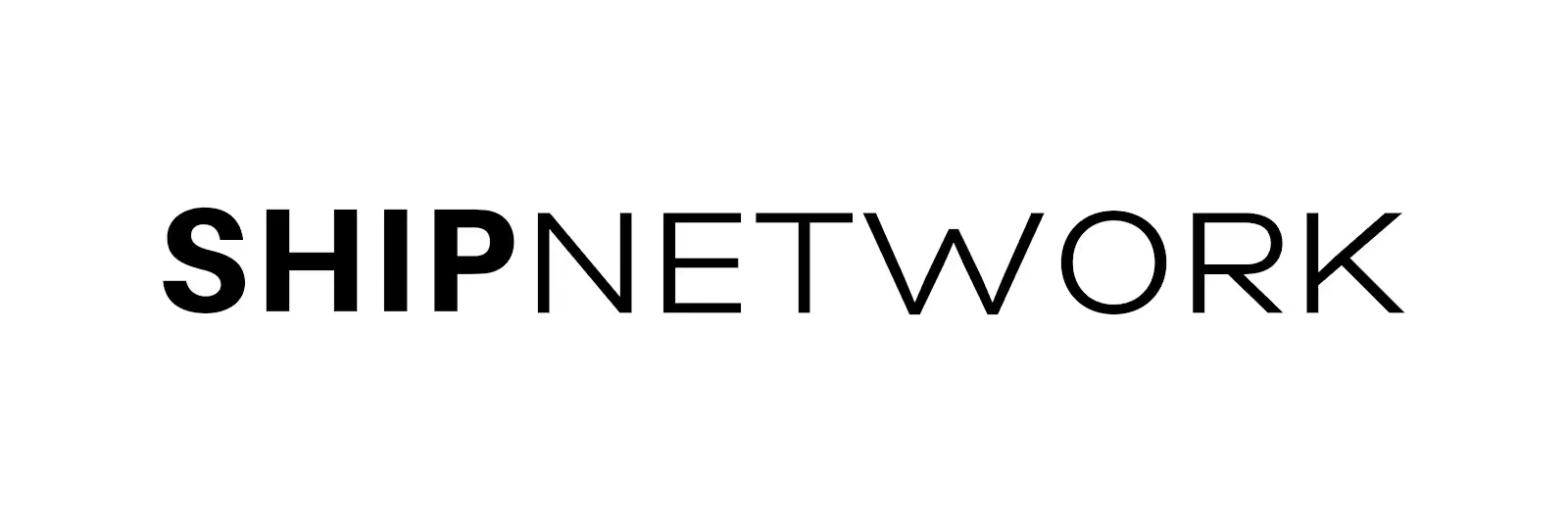
Delivering a problem-free shopping experience to customers is the top priority for any online retailer. However, even the most well-organized retail outlets sometimes have trouble promptly and accurately filling customer orders. You can streamline your logistics management with the help of ShipNetwork's knowledge of EDI codes for 3PLs and warehousing.
You can now easily send information about orders, shipments, and data with the help of EDI transaction codes that are commonly used across the industry. Additionally, you can easily track your shipping operations and view real-time analytics with the help of ShipNetwork’s user-friendly dashboard.
Reduce errors and streamline logistic operations for eCommerce by using the right EDI codes and sending the necessary info with ShipNetwork’s experts. Contact Us today to learn more.